Houten huizen met een zuiverheidseis
Een expertproject van friedl holzbau gmbh
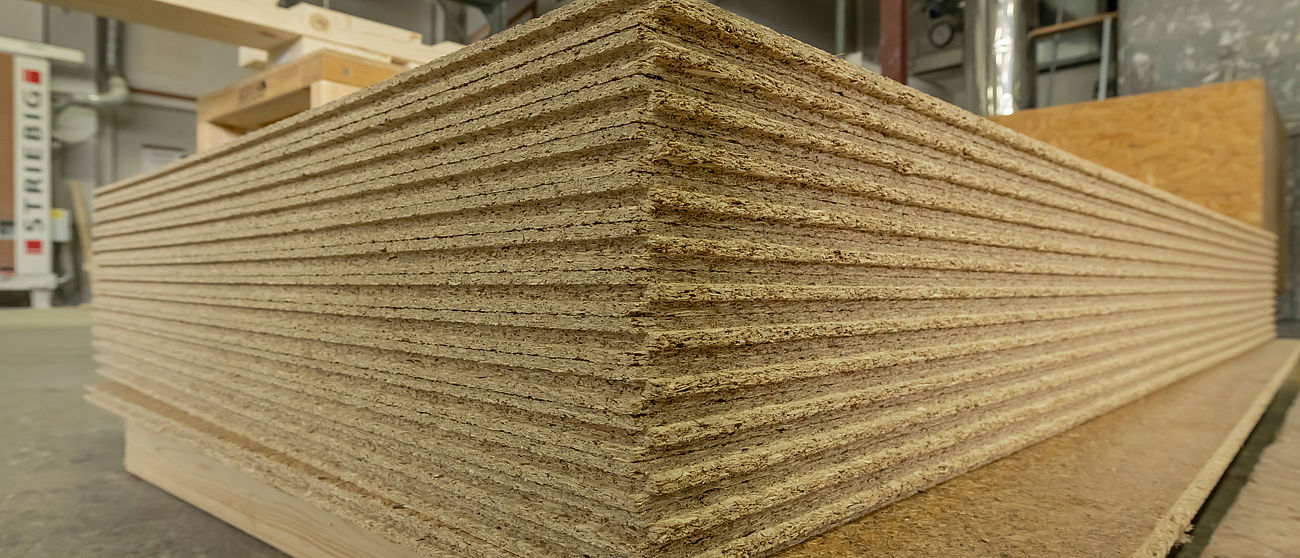
Om redenen van woongezondheid gebruiken wij LivingBoard van Pfleiderer voor ons Friedl Holzwerthaus. - Richard Schinagl Jr.
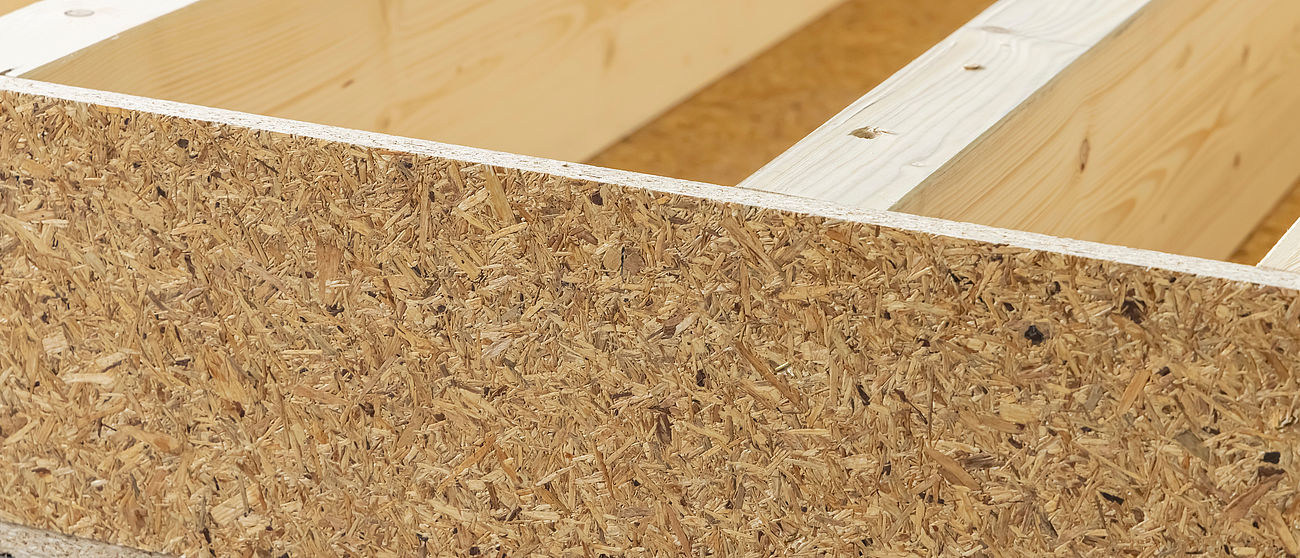
Om redenen van woongezondheid gebruiken wij LivingBoard van Pfleiderer voor ons Friedl Holzwerthaus. - Richard Schinagl Jr.
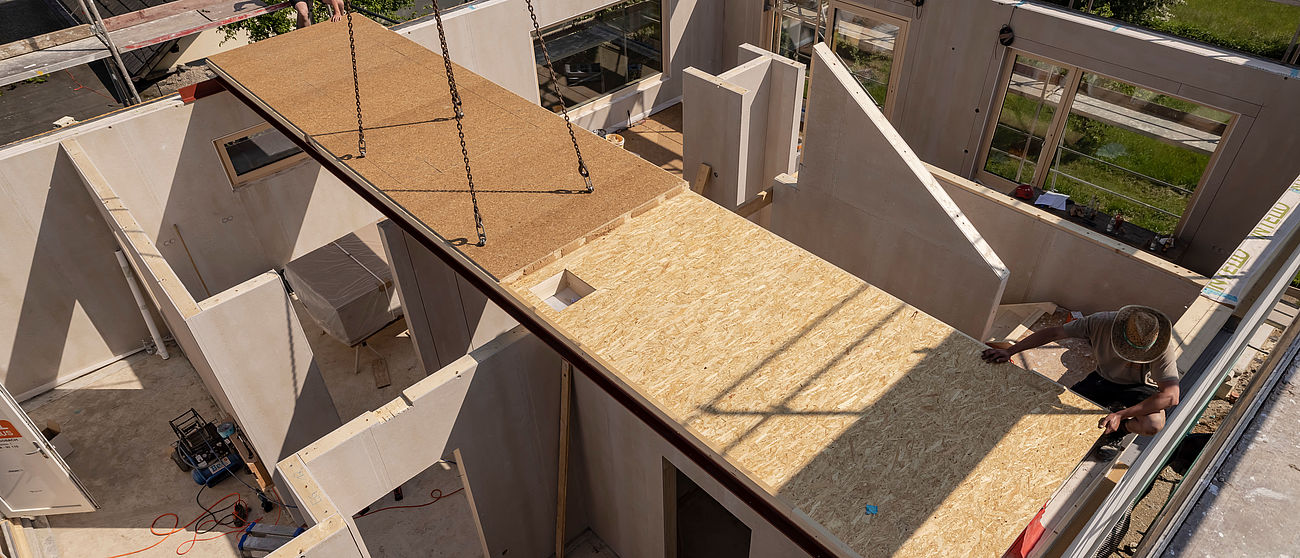
Om redenen van woongezondheid gebruiken wij LivingBoard van Pfleiderer voor ons Friedl Holzwerthaus. - Richard Schinagl Jr.
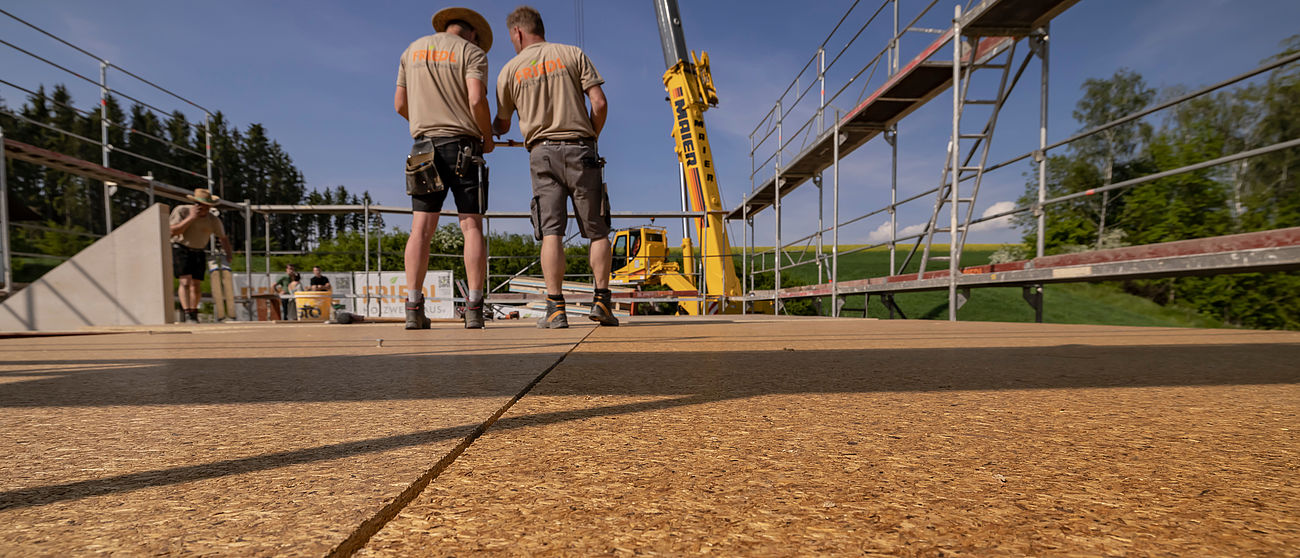
Om redenen van woongezondheid gebruiken wij LivingBoard van Pfleiderer voor ons Friedl Holzwerthaus. - Richard Schinagl Jr.
Pfleiderer in gesprek met dhr Richard Schinagl jr.
Pfleiderer: Mijnheer Schinagl, wat moeten we ons voorstellen bij een Holzwerthaus?
Richard Schinagl: Een Friedl Holzwerthaus is ons antwoord op de vraag hoe je een geprefabriceerd houten huis beter kunt maken. Het begint al met de naam. Want bijna alle moderne houten huizen die in het zuiden van Duitsland gebruikelijk zijn, worden gebouwd met behulp van houtskeletbouw of houtpaneelbouw. Omdat de elementen geprefabriceerd zijn, zijn het natuurlijk geprefabriceerde huizen in de letterlijke zin van het woord. Maar als ze de term "prefab huis" horen, denken sommige mensen intuïtief aan "prefab pizza", d.w.z. niet zulke hoogwaardige massaproducten, en dat is waar wij ons juist willen positioneren.
Pfleiderer: Beschrijf alstublieft uw filosofie.
Richard Schinagl: Ten eerste is het belangrijk voor ons om te benadrukken dat wij geen kant-en-klare huizen bouwen. Dit betekent dat onze klanten altijd een huis op maat krijgen, waarbij ze zelf invloed kunnen uitoefenen op de geometrie en de indeling van de kamers. Op de achtergrond gebruiken we natuurlijk ook gestandaardiseerde modules, maar deze geven ons een hoge mate van flexibiliteit bij het samenstellen ervan. Hierdoor kunnen we de economische voordelen van systeembouw optimaal combineren met de wensen van onze klanten. Voor ons resulteert dit in een intensieve plannings- en overlegfase voor elk van de ongeveer 30 huizen die wij elk jaar realiseren.
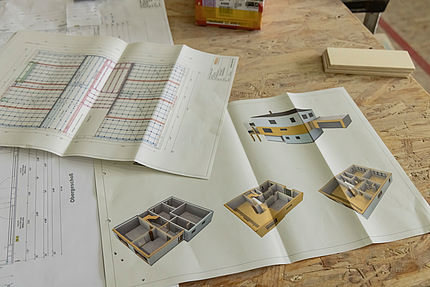
Pfleiderer: U zou dat allemaal zeker ook met andere bouwmaterialen kunnen doen. Waarom hout?
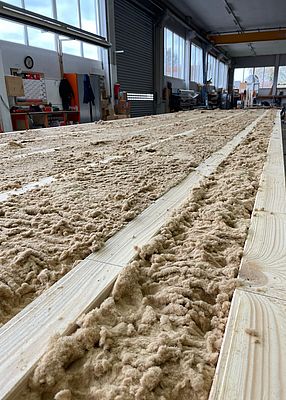
Richard Schinagl: Het past gewoon perfect in onze kwaliteitsfilosofie. Iedereen die tegenwoordig een huis bij ons bouwt, hecht veel belang aan ecologie en gezond leven. Dit werkt het beste met hout. Wij hebben dit als een kans gezien om ons van de concurrentie te onderscheiden en zijn daarom geleidelijk overgeschakeld op de gezondste en duurzaamste alternatieven voor onze materialen.
Neem bijvoorbeeld onze wandstructuren: Waar we vroeger OSB en mineraalwolisolatie en polystyreen met hoge dichtheid gebruikten, hebben we het aandeel hout geleidelijk en consequent verhoogd: eerst hebben we het polystyreen op de gevel vervangen door een plaat van zachte houtvezels. Vanwege de thermische isolatievereisten hadden we echter ook een dikker compartiment nodig. Tegelijkertijd nam de dikte van de muurstijlen toe van 16 tot 24 cm. We vervingen ook de OSB-platen door LivingBoard van Pfleiderer om redenen van woongezondheid. Vervolgens zijn we van minerale wolisolatie in de compartimenten overgestapt op Isofloc inblaasisolatie. Maar niet met cellulosevezels, d.w.z. hun standaardproduct, maar met houtvezels. Wij waren pioniers in het voor de eerste keer gebruiken van de inblaasmachine met het losse houtvezelisolatiemateriaal en het duurde even voordat alles soepel liep. Maar nu bereiken we naast de gewenste thermische isolatie ook een betere geluidsisolatie.
Onze muur bestaat nu voor bijna 100% uit natuurlijke, gezonde materialen, het meeste daarvan is hout. We hebben zelfs een natuurlijke oplossing gevonden voor de plekken waar het risico op vocht bestaat, zoals de onderkant van het gebouw en de raamaansluitingen, namelijk speciale isolatiepanelen van kurk.
Pfleiderer: Nogal wat moeite, maar je ziet het niet aan de muur, of wel?
Richard Schinagl: Ja, maar dat is gewoon onze houding of onze aard. We ontwikkelen totdat we zelf helemaal tevreden zijn. Dat duurt een tijdje, en dan komt de volgende fase, waarin het nog beter moet. Natuurlijk maakt deze neiging tot perfectionisme het leven niet altijd gemakkelijk, vooral in een industriële omgeving die in vergelijking wat ruwer is. Maar dat is de prijs die we betalen voor onze zelfopgelegde "zuiverheidseisen" [grinnikt].
Het feit dat onze muren, die tot in het kleinste detail geoptimaliseerd zijn, vervolgens in de meeste gevallen volledig bepleisterd worden, is natuurlijk ongunstig vanuit marketingoogpunt. Om ervoor te zorgen dat de hoogwaardige natuurlijkheid van het huis op het eerste gezicht nog steeds zichtbaar is, gebruiken we hout-aluminium ramen en enkele houten gevelelementen, die het duurzame interieur dan zichtbaar aanvullen.
Pfleiderer: Hoe moeten we de productie van de muur die u net beschreef visualiseren?
Richard Schinagl: Wij werken industrieel in de meest positieve zin van het woord. De planning is volledig digitaal en we gebruiken ultramoderne machines en duidelijk gedefinieerde processen om maximale precisie te bereiken. De modules worden in onze fabriek geprefabriceerd en ter plaatse gemonteerd. Op deze manier zorgen we ervoor dat de wensen van onze klanten precies worden gerealiseerd. Aan de andere kant maakt de hoge mate van mechanisatie de productie ook efficiënter vanuit kostenoogpunt. Zowel ecologie als digitalisering zijn fascinerend, maar mogen naar mijn mening geen doel op zich worden. Voor onze klanten, en voor ons, moet de resulterende waarde juist zijn. Met andere woorden, het hele pakket van comfort en esthetiek tot woongezondheid, duurzaamheid en lange levensduur!
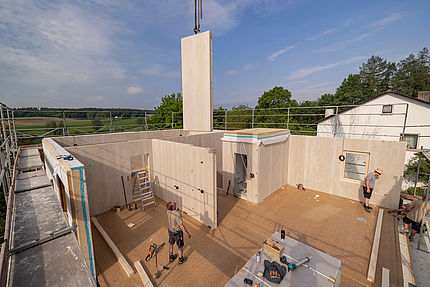
Pfleiderer: Als relatief klein bedrijf met een hoge mate van maatwerk maakt Friedl toch gebruik van showhuizen. Waarom is dat?
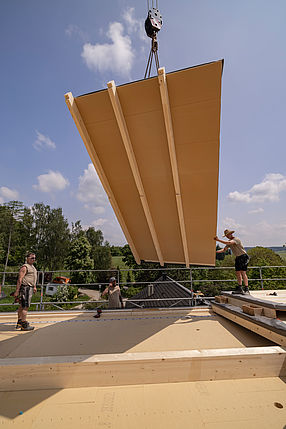
Richard Schinagl: Wij bouwen huizen voor mensen en wij mensen zijn allemaal wezens van vlees en bloed en communiceren via onze vijf zintuigen. Je hebt gewoon iets tastbaars nodig om aan te raken en te voelen. In tegenstelling tot wat vaak gedacht wordt, zijn onze showhuizen echter geen gestandaardiseerde huizen die alleen gekocht kunnen worden zoals ze zijn, maar zijn het gewoon pronkstukken die bedoeld zijn om de kwaliteit van een FRIEDL Holtzwerthaus te demonstreren.
De modelwoning geeft ons ook de mogelijkheid om nieuwe systemen zelf onder echte omstandigheden te testen, zonder risico voor onze klanten. Daarom hebben we nu na 9 jaar een nieuw showhuis gebouwd, hoewel het oude in veel opzichten nog prima in orde is. In ons nieuwe huis hebben we ons, naast de nieuwe muurconstructies, ook gericht op het onderwerp energievoorziening. Met een lucht/water-warmtepomp en fotovoltaïsche energie bieden we een toekomstbestendige verwarmingsoplossing waarvoor geen fossiele brandstoffen nodig zijn. We hebben ook het zogenaamde BayWa klimaatplafond gebruikt en doen daar nu ervaring mee op. Dit is een geprefabriceerd systeem dat aan het plafond wordt geïnstalleerd en de kamers naar behoefte verwarmt of koelt.
De voordelen voor de bewoners zijn duidelijk. Maar het biedt ons ook een nieuwe kans om onze huizen iets slimmer te bouwen. Tegelijkertijd maken we van de gelegenheid gebruik om voor het eerst een droge dekvloer te testen. Als deze twee systemen zich bewijzen, en ik ga ervan uit dat dat zal gebeuren, kunnen we de energie-efficiëntie en het comfort verbeteren en de bouwtijd verkorten omdat we de droogfase voor de dekvloer uitsparen. Dit zijn ontwikkelingen die helemaal in mijn straatje passen!
Pfleiderer: Is een Friedl Holzwerthaus ook sneller klaar dankzij al deze ontwikkelingen?
Richard Schinagl: In principe wel. Vanaf het begin van de ontwerpplanning tot het moment dat het huis klaar is om in te trekken, rekenen we op een totale ontwikkelingstijd van driekwart tot een heel jaar, met een pure bouwtijd op het perceel van drie tot vier maanden. We kunnen de bouwtijd echter nog verder inkorten door gebruik te maken van de droge dekvloer die hierboven is genoemd.
En voor het eerst hebben we in ons showhuis ook een hele kamer, de kinderbadkamer, geprefabriceerd als een driedimensionale kamercel, compleet met alle installaties, tegels en afgewerkte oppervlakken, en deze kamermodule vervolgens vanuit de werkplaats samen met de andere geprefabriceerde elementen van het huis gemonteerd. Dit bespaart natuurlijk tijd en helpt ons om het werk in de werkplaats beter onder controle te houden.
Bovendien worden veel van onze huizen, vooral die op landelijke locaties waar ruimte geen probleem is, nu zonder kelder gebouwd. Aangezien de bouwtechnologie steeds compacter wordt, is dit voor ons nog een manier om de bouwkosten te verlagen zonder dat de klant ongewenste compromissen hoeft te sluiten. Zoals u ziet, streeft onze filosofie er altijd naar om zoveel mogelijk factoren te optimaliseren en perfect op elkaar af te stemmen: Esthetiek, woongezondheid, duurzaamheid en - last but not least - een goede prijs-prestatieverhouding. Wij zijn pas tevreden als dit alles klopt en het huis van onze klanten een echt Friedl Holzwerthaus is!
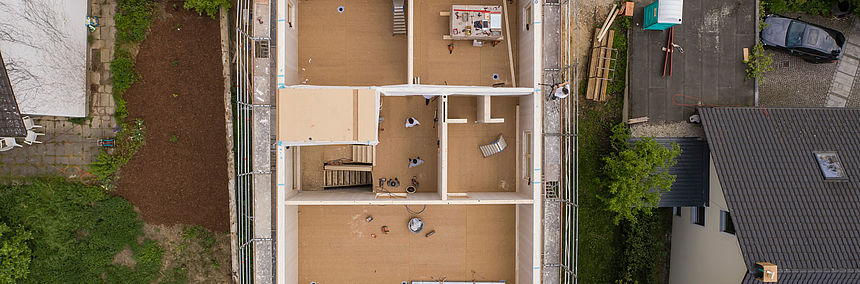
Pfleiderer: Meneer Schinagl, bedankt voor het interview!
PROFIEL RICHARD SCHINAGL JR.
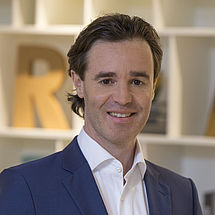
Beroep | Burgerlijk ingenieur & algemeen directeur |
Motto | Leven en laten leven, de beste oplossingen zijn het resultaat van vrije concurrentie |
De feiten over het project
Project: | Showhuis Friedl Holzbau GmbH Niedersüßbach |
Product: | LivingBoard Face Contiprotect P5 StyleBoard MDF.RHW |
Toepassingsgebied: | Houtskeletbouw in wanden en plafonds |
Uitvoering: | FRIEDL Holzbau GmbH Johannesstraße 1 - Niedersüßbach 84101 Obersüßbach |
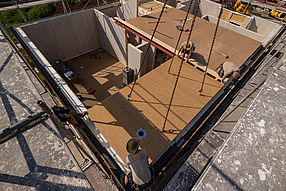
Klant: | FRIEDL Holzbau GmbH Johannesstraße 1 – Niedersüßbach 84101 Obersüßbach |
Voltooiingsdatum: | Augustus 2023 |
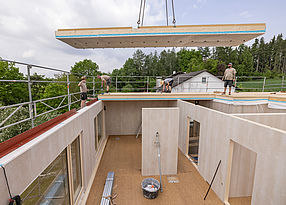
Gebruikte Producten
INDIVIDUELE BEGELEIDING
Neem contact met ons op
Neem direct contact met ons op! We horen graag van je.
Productaanvragen en verkoop.
+49 (0) 9181 28-480