Building the future – module by module!
An Experts project from Timber Homes - Raummodule
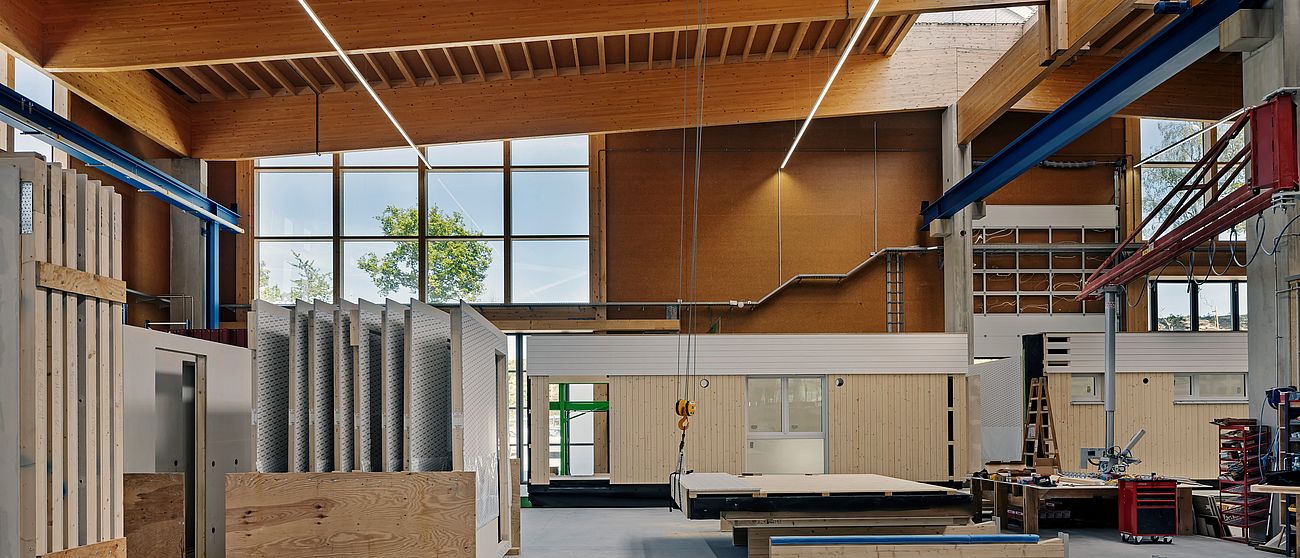
The factory building in Dorfen perfectly illustrates the advantages of constructing commercially used buildings from timber: we have realised sustainability in a way that is as economical and functional as the room modules that we produce here!
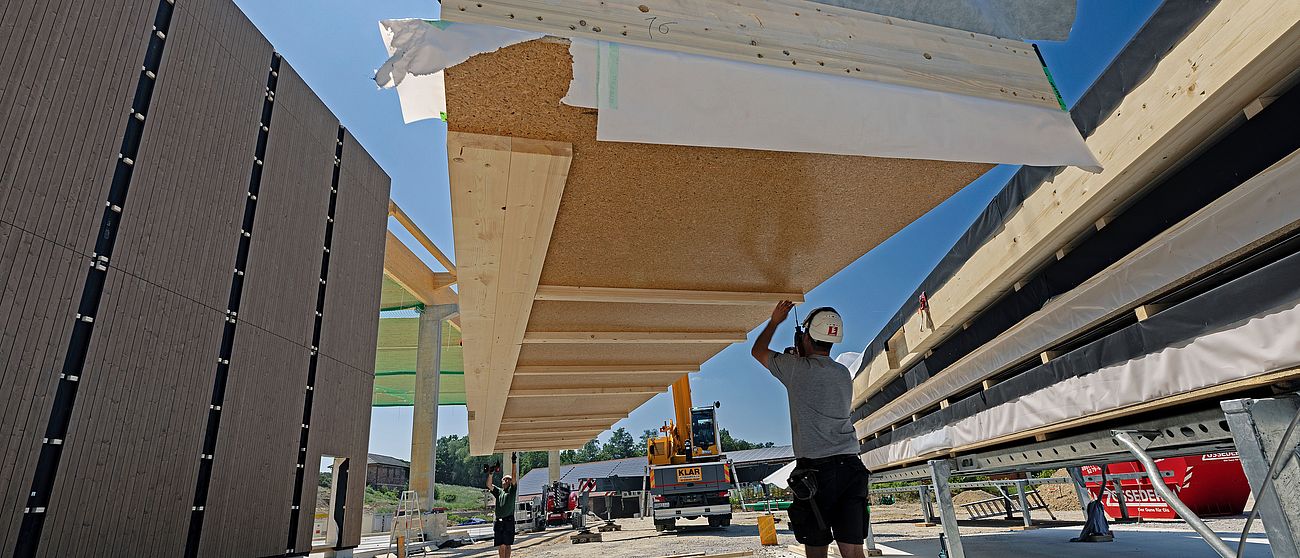
The factory building in Dorfen perfectly illustrates the advantages of constructing commercially used buildings from timber: we have realised sustainability in a way that is as economical and functional as the room modules that we produce here!
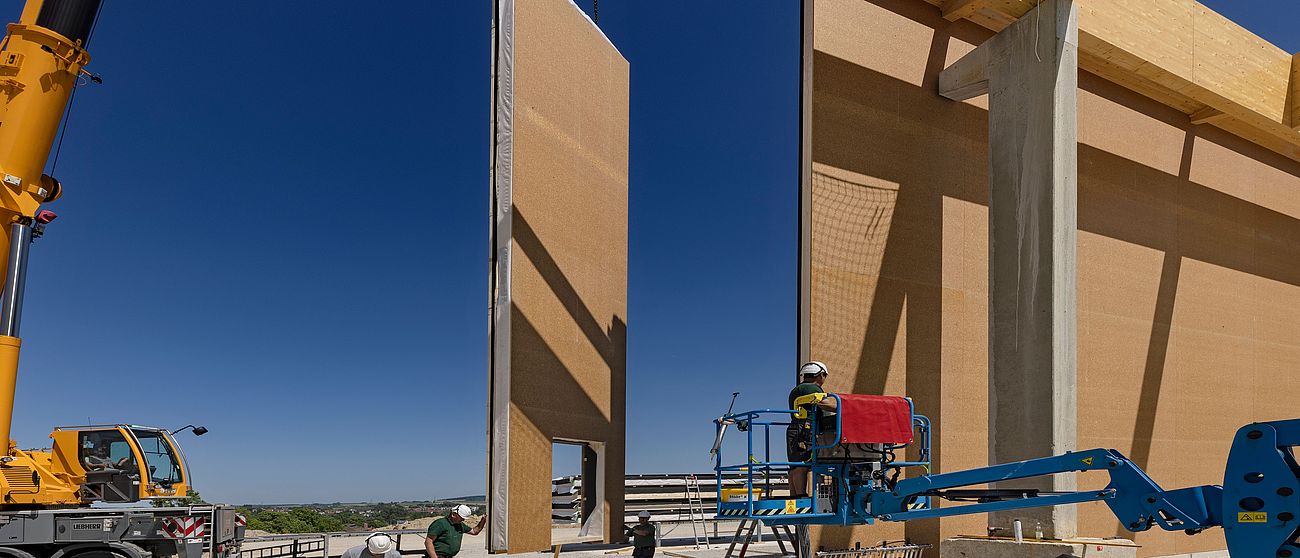
The factory building in Dorfen perfectly illustrates the advantages of constructing commercially used buildings from timber: we have realised sustainability in a way that is as economical and functional as the room modules that we produce here!
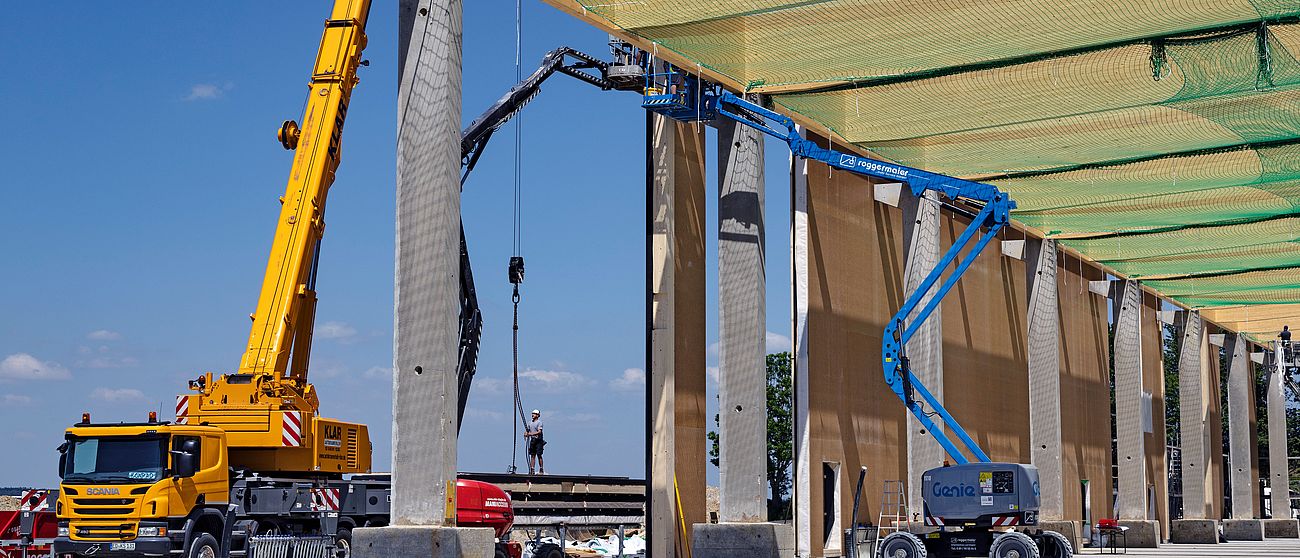
The factory building in Dorfen perfectly illustrates the advantages of constructing commercially used buildings from timber: we have realised sustainability in a way that is as economical and functional as the room modules that we produce here!
Pfleiderer in conversation with Mr. Hangl and Ms. Rieder
Pfleiderer: Ms Rieder, what requirements were stipulated by the building's owner did you have to meet when you started to plan the project?
Monika Rieder: The new factory was built on the site of a former brickworks. It was important to the client to build both sustainably, as well as economically. Timber Homes already used the grounds in the past; the construction of the new factory represents an important building block for the company in terms of its future development. The building was to instantly communicate that Timber Homes works with wood. Obviously, this had a direct impact on the construction method and the choice of materials.
Pfleiderer: How did you meet these requirements? And what makes the factory special?
Monika Rieder: The factory was built on top of the foundations of the former brickworks' old drying shed. We used the brickworks' supports and added a new support axis in the centre. On the inside, the space is divided in two, lengthways. On the one side is a rail system on which the timber construction modules are conveyed along the production line. If necessary, they can be "redirected" away from the line and pushed to holding positions at the other side of the space. This happens when individual fitting stages take longer than scheduled. Other than that, the other side of the factory is designed for use as a material store where the fit out materials are stored within easy reach of the production stations. In some parts, this half also features a mezzanine level so that the space can be used even more flexibly.
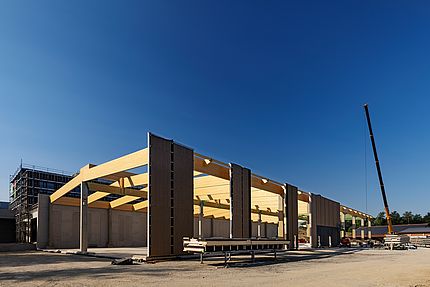
Pfleiderer: Mr Hangl, you are associated with this building in two ways. Could you please explain this?
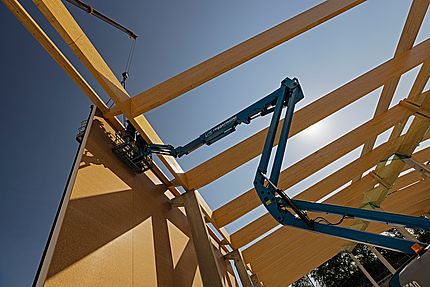
Christian Hangl: On the one hand, my company holds shares in Timber Homes. This means that we are actively involved in the development, manufacture and installation of the Timber Homes timber modules. As Huber & Sohn, we prefabricate the wall elements that are assembled into room modules at Timber Homes. On the other hand, we were the company commissioned with the realisation of Ms Rieder's plans for the construction of the new factory building.
Pfleiderer: So this means that complete modular rooms are manufactured inside the new factory?
Christian Hangl: Yes, exactly. The factory is designed to be able to handle module lengths of up to twelve metres; we are currently manufacturing modules that are up to nine metres long there. From the construction of the basic structure to the turnkey interior fit out, everything is done in Dorfen. The modules are then transported to the construction site, and the final assembly is finished on location. They are used to create larger residential buildings, commercial properties or extensions to existing buildings. The project we are realising in cooperation with Hotel & Apart4you directly in our grounds is a prime example: 53 modern apartments that can sleep 125 in total are currently under construction here – and they are being constructed exclusively from prefabricated room modules.
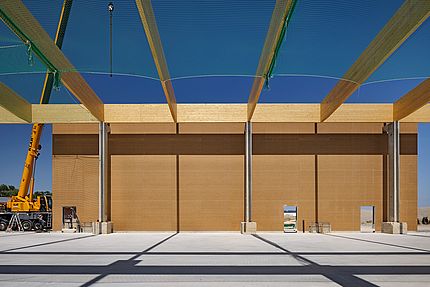
Pfleiderer: What are the advantages of this construction method, Mr Hangl?
Christian Hangl: Primarily – besides the ecological aspects – speed. The ground-breaking ceremony for the apartments was held in February; they are scheduled to be open for business in July 2024. Through precise industrial prefabrication, we can minimise the installation time and effort on the construction site. By doing it this way, we are also largely independent of the weather. The planning permission process is also much easier and quicker. And in theory, we could also dismantle our modules at our factory at the end of a building's life cycle. In future, this aspect will also become increasingly important when it comes to eco-friendly or climate-conscious construction. The Timber Homes modular construction method therefore offers a range of benefits to developers who want to build high-quality and sustainable buildings, and who want to build them fast.
Pfleiderer: The factory is also based on an innovative construction principle. Could you please explain this in more detail, Ms Rieder?
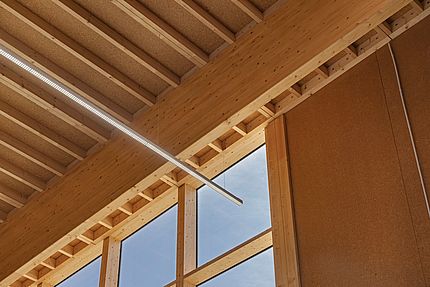
Monika Rieder: Well, first of all, there is the already mentioned requirement that the fact that the company works in timber construction was to be obvious at first glance. In addition, we built the factory on the existing foundation slab, for economical reasons. We were also tasked with creating a modern, bright and friendly working environment in order for the company to be considered as an attractive employer in these times of an increasing shortage of qualified staff. Dividing the interior in two played an important role with regard to the efficient use of the available space. Expansive windows let plenty of daylight into the production area, and a supporting structure of glulam trusses resting on reinforced concrete supports creates a generousness in the layout that meets the requirements of the work processes, but also contributes to the comfortable ambience inside the factory. Many other construction details have also been cleverly solved using timber, such as the protection barriers for the forklift truck that is used to move the room modules, for example: we managed to integrate these into the supports running along the sides of the gates. Not an easy task, considering that the modules that are being moved here weigh up to fifteen tons. However, in this way, we were able to do without the usual collision barriers that jut out and would have spoilt the factory's overall aesthetics.
Pfleiderer: However, the factory speaks for timber construction not only in aesthetic terms. Could you elaborate the construction method further?
Christian Hangl: The roof construction consists of a twelve-metre grid of solid wood trusses that has been reinforced with 22mm thick LivingBoard P7. The façade consists of wall elements that are 12.3 metres high. The exterior walls feature a solid timber frame with a 320mm thermal insulation layer filled with mineral wool. Towards the inside, they have been sheathed in 22mm thick LivingBoard P7– just like the roof, too. For this type of construction, it was a major advantage for us that Pfleiderer was able to supply the panels preconfigured to 2580 x 6000mm, as this perfectly matches the twelve-metre grid of the trusses and made it possible to sheathe the interior with minimum waste. The outer layer of the building's exterior is formed by Fermacell fibre gypsum boards; on top, a solid wood façade has been created with vertical tongue and groove cladding. This construction method made it possible for us to achieve a perfect balance between meeting the economical and structural requirements and creating the desired comfortable workplace atmosphere.
Monika Rieder: In addition, the client applied high sustainability standards when it came to the conversion of the old brickworks. In part, we therefore even reused construction materials from the previous buildings for other purposes within the grounds. A Cradle to Cradle silver certified board such as LivingBoard perfectly suited the material concept, which aimed for recyclability. The new factory is also part of a well-thought-out, resource-saving concept when it comes to the energy supply: a small-scale local district heating system in the grounds is used to supply all buildings efficiently with sustainably generated heat. In addition, there are numerous solar panels on top of the buildings – including the Timber Homes factory – that generate a not insignificant amount of the electricity required directly on site.
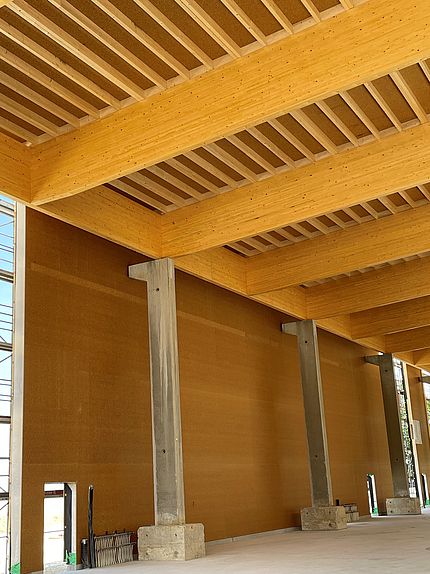
Pfleiderer: What role does sustainability play in the Timber Homes products, i.e. the room modules?
Christian Hangl: Our modular buildings contribute to a sustainable construction carbon footprint: the wood used to construct them captures carbon, they are characterised by good insulation values and are equipped with controlled living space ventilation, including heat recovery. They also benefit from a self-sufficient energy concept with a PV system and battery storage. They are therefore eligible for subsidies under Germany's KfW40+ energy standard subsidy scheme – and impressively demonstrate the future of sustainable, economical construction and living.
Pfleiderer: How many modules can you build at the site in Dorfen?
Monika Rieder: The factory is designed in such a way that ten to fifteen modules can run through the production process simultaneously. Currently, during the start-up phase, one module is being completed per day; the capacity is then scheduled to be increased to three modules a day . For Timber Homes, the new factory building is therefore a decisive building block for putting the corporate goals that are on the agenda for the next few years into practice.
Christian Hangl: The fact that Germany's Federal Minister for Housing, Urban Development and Building Klara Geywitz attended the factory opening ceremony in February 2024 in person also indicates the increasing importance of sustainable timber construction on an industrial scale. It was a great honour for us, and proves that we are making a genuine contribution to the responsible use of natural resources with our work and our concept, and therefore ultimately to a viable future.
Pfleiderer: Ms Rieder, Mr Hangl, thank you very much for the interview!
Profile MONIKA RIEDER & CHRISTIAN HANGL
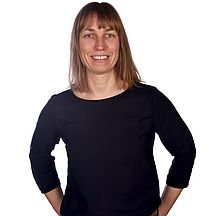
„Always remain curious and embrace new challenges.“
Monika Rieder
Architect
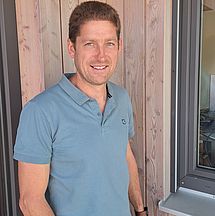
„Pushing interesting projects, developing new constructions, and always trying to be one step ahead.“
Christian Hangl
Construction engineer & master joiner
Information box
Construction project: | Timber Homes factory, Dorfen, Germany |
Developer: | Timber Town Immobilienmanagement GmbH & Co. KG |
Product: | LivingBoard Face Contiprotect P7 |
Planning: | Monika Rieder, Rieder Architektin + Stadtplaner PartG mbB, Obing |
Timber construction realisation: | Huber & Sohn GmbH & Co. KG, Bachmehring |
Completion: | 2024 |
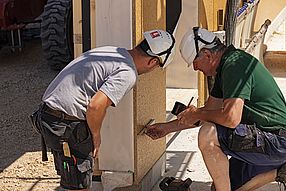
Products used
INDIVIDUAL ADVICE
Contact
Please get in touch with us directly! We look forward to hearing from you.
Product inquiries and sales.
+49 (0) 9181 28-480