OBJECTIF 1
AUGMENTER LE RENDEMENT TOTAL DU BOIS UTILISÉ POUR LA PRODUCTION DANS CHAQUE USINE, POUR ATTEINDRE AU MOINS 90 % D'ICI 2025.
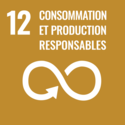
Notre rendement en bois, un indicateur de performance important, ne cesse de s'améliorer : en 2020, nous avons atteint dans nos usines des taux compris entre 82 et 94 % pour l'ensemble du mélange de bois. Grâce à des innovations continues dans le domaine du tri et de la détection des impuretés, ainsi qu'à des investissements concrets dans ces domaines, nous estimons qu'un taux de 90 % est techniquement réalisable d'ici 2025 pour toutes nos usines. Pour les usines qui ont déjà atteint un rendement supérieur à 90 %, notre objectif est de le maintenir. En 2024, nous avons pu atteindre un rendement total du bois compris entre 87 et 92 % selon les usines (2020 : 82 à 91 %). Un rendement de 100 % n'est physiquement pas possible, car le bois recyclé utilisé contient toujours certains composants indésirables.
RENDEMENT TOTAL DU BOIS : NOS PERFORMANCES ET OBJECTIFS
2020 | 2021 | 2022 | 2023 | 2024 | Valeur cible 2025 | |
Rendement technique du bois en % | ||||||
Usine avec la plus haute valeur | 91,1 | 91,3 | 91,8 | 91,1 | 91,7 | 90,0 |
Usine avec la valeur la plus faible | 81,8 | 83,4 | 82,5 | 84,3 | 86,9 | 90,0 |
OBJECTIF 2
AUGMENTER À 50 % LA PART DE BOIS RECYCLÉ POST-CONSOMMATION D'ICI 2025.
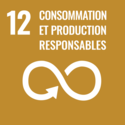
Nous sommes les plus grands utilisateurs de bois usagé en Allemagne. Nous utilisons cette force, pour promouvoir de manière systématique l'utilisation en cascade du bois. Nous contribuons ainsi à limiter le gaspillage et à favoriser l’économie circulaire. Cela signifie qu’après avoir été utilisés une première fois, les produits dérivés du bois sont traités autant que possible comme des matières premières précieuses. Ils ne sont ainsi utilisés comme combustible qu’à la fin de leur cycle de vie. Nous souhaitons que tous les produits en bois soient recyclés. Cela inclut nos propres rebuts de production.
Le bois recyclé post-consommation représente 53,5 % du mélange de bois utilisé dans tous nos produits.1 Grâce à la mise en œuvre cohérente de notre stratégie de recyclage, nous avons déjà atteint avant l'échéance l'objectif de 50 % que nous nous étions fixé pour 2025. La deuxième fraction la plus importante est constituée à 25 % de résidus de sciage. Les 21 % restants proviennent de l'éclaircissage et du bois de rupture issus de la sylviculture contrôlée en Allemagne et dans les pays voisins directs.
1 Nos matériaux post-consommation se réfèrent au bois de recyclage préparé provenant de palettes endommagées, d'emballages, de meubles ou de cuisines usagées, ainsi que les déchets internes ; ces derniers ne représentent que 2,5 % du total du bois recyclé.
Bois recyclé : nos performances et objectifs
2020 | 2021 | 2022 | 2023 | 2024 | Valeur cible 2025 | |
Pourcentage de bois recyclé dans notre mix de bois | 41.7 | 46.2 | 48.1 | 50,7 | 53,5 | 50.0 |
De nombreux facteurs influent sur la quantité disponible de bois recyclé : les initiatives de réutilisation et de recyclage dans l'Union européenne, le développement économique, le comportement des consommateurs et la valorisation des meubles usagés par les détaillants en ameublement. Notre approche stratégique de la durabilité implique également un dialogue avec d'autres parties prenantes, pour nous aider à atteindre cet objectif. Nous pouvons augmenter la quantité de bois usagé disponible, en influençant le comportement des consommateurs et des entreprises.
Même si nous souhaitons traiter du bois recyclé en grandes quantités, nous n’acceptons que des matériaux de la catégorie la plus haute pour notre production. Nos panneaux sont régulièrement contrôlés dans notre laboratoire central d'Arnsberg et nous collaborons avec nos fournisseurs pour veiller au respect strict de nos normes de qualité.
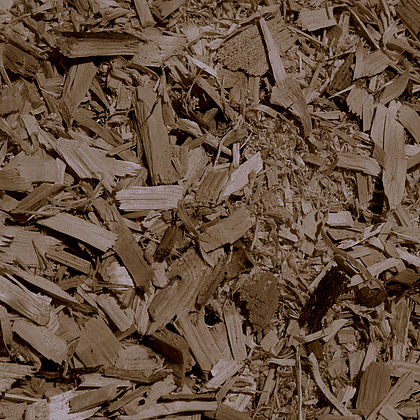
80% DES MATIÈRES PREMIÈRES BOIS UTILISÉES DANS NOS PRODUITS SONT DES RÉSIDUS DE SCIERIE ET DU BOIS RECYCLÉ.
Exemple pratique
Tri, nettoyage et contrôle du bois recyclé
Notre rendement élevé reflète la qualité de notre matière première la plus importante : le bois recyclé. Une fois le matériau livré à l'usine, nous voulons éviter autant que possible les pertes lors du nettoyage. Le rendement très élevé de nos sites (90 % en moyenne) est le résultat de nos investissements continus dans des technologies de pointe. Nos processus de tri et de nettoyage, nos relations avec nos fournisseurs et nos procédures de contrôle strictes sont des facteurs de succès déterminants. La « tour de tri » garantit qu'aucun matériau indésirable, tel que du plastique, ne pénètre dans nos lignes de production. En fait, nous repoussons sans cesse les limites du possible pour maximiser le rendement. Grâce au nombre élevé de processus de tri, nous disposons de fractions de matières premières de plus en plus fines. L'utilisation multiple de fibres de bois recyclées nous permet également de réduire notre dépendance vis-à-vis des sous-produits de la sylviculture.
OBJECTIF 3
PRODUIRE, D'ICI 2025, 10 % DE NOS MATÉRIAUX À BASE DE BOIS, EN UTILISANT UNE PROPORTION DE LIANTS BIOSOURCÉS
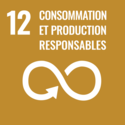
Notre site de production nous permet de traiter environ 250 000 tonnes de résines, liants, additifs et vernis par an. Afin de remplacer une partie de ces matières premières par des matières premières renouvelables, nous poursuivons un objectif concret : d'ici 2025, nous voulons fabriquer 10 % de nos produits à base de bois (en volume) en utilisant une proportion de résines biogènes. En 2024, nous avons lancé OrganicBoard Pure, un liant 100 % renouvelable et biogène.
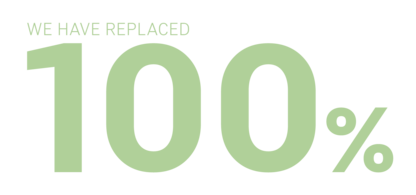
... DES COLLES FOSSILES ONT ÉTÉ REMPLACÉES PAR DE L'ORGANICGLUE RENOUVELABLE DANS NOTRE PRODUIT ORGANICBOARD PURE. ORGANICBOARD PURE EST UN PANNEAU DE PARTICULES AVEC 100% DE LIANT RENOUVELABLE ET 100% DE BOIS RECYCLÉ.
OBJECTIF 4
DÉVELOPPEMENT DE KPIS SPÉCIFIQUES POUR L'EAU ET LES DÉCHETS, SELON LES NORMES DU GRI
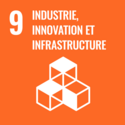
En tant qu'entreprise spécialisée dans l'élimination des déchets, nous minimisons les déchets en recyclant le bois usagé sous forme matérielle et thermique. Malgré notre approche très stricte en matière de recyclage du bois, nous produisons néanmoins des déchets sous forme de cendres, d’emballages et de résidus.
Gérer les déchets non évitables
Nous ne disposons pas de décharges sur nos sites. Heller Holz GmbH, ainsi que les installations de cogénération installées sur nos sites de Neumarkt, Gütersloh et Baruth, sont certifiées pour l’élimination des déchets. Elles répondent à de nombreuses exigences en la matière.
En tant que membre de l’association allemande des matières premières secondaires et de la gestion des déchets, Pfleiderer contribue à la mise en œuvre d’une utilisation en cascade du bois, dans le respect des réglementations légales, telles que celles sur le bois usagé.
En 2023, nous avons dÉveloppÉ un systÈme de reporting des dÉchets, pour mieux gÉrer et rÉduire les flux de dÉchets.
Ce système comprend un module de saisie automatique pour la catégorisation des déchets détournés de l'élimination. Il inclut les processus de réutilisation, de recyclage et autres valorisations, tant pour les déchets dangereux que pour les déchets non dangereux. En outre, le système dispose d'un enregistrement automatique pour les déchets destinés à être éliminés. Cela inclut l’incinération (avec ou sans valorisation énergétique), la mise en décharge et autres possibilités d’élimination, tant pour les déchets dangereux que pour les déchets non dangereux.
EAU
Après validation de notre analyse d'importance, nous avons redéfini les priorités du thème de l'eau en tenant compte de notre impact. Bien que la plupart de nos sites soient situés dans des régions riches en eau, nous sommes conscients que la pénurie d'eau est un problème mondial aggravé par la crise climatique. C'est pourquoi la gestion de cette ressource revêt une importance stratégique croissante pour nous.
GESTION DE L‘EAU
Nous nous sommes engagés à gérer la ressource en eau de manière responsable et nous sommes en train de documenter nos besoins en eau de manière transparente. Cette documentation est une condition préalable, pour être en mesure d’adapter notre gestion de l'eau aux variations de disponibilité attendues, en raison du changement climatique.
OBJECTIF 5
ÉLABORATION D'UN PLAN DE GESTION DE LA BIODIVERSITÉ D'ICI 2025 POUR TOUS LES SITES DE PRODUCTION SITUÉS DANS OU À PROXIMITÉ DE RÉSERVES NATURELLES.
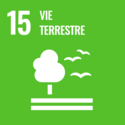
La biodiversité est un sujet stratégique important pour notre entreprise. Nous avons analysé notre impact sur la biodiversité par le biais de la plateforme publique Contrôle de la biodiversité , soutenue par le ministère allemand de l'Environnement. Nous avons évalué ces impacts pour les terres dont nous sommes propriétaires et pour celles que nous louons et gérons, ainsi que tout au long de la chaîne d'approvisionnement. Selon les résultats obtenus, notre entreprise a un impact important sur la biodiversité et elle peut le réduire nettement en prenant des mesures appropriées. L'analyse se poursuit et nous devons encore définir des indicateurs appropriés.
OBJECTIF 6
IDENTIFICATION ET ATTÉNUATION D'ICI 2025 DES IMPACTS NÉGATIFS POTENTIELS SUR LA BIODIVERSITÉ TOUT AU LONG DE NOTRE CHAÎNE D'APPROVISIONNEMENT EN BOIS.
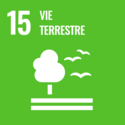
Nous n’utilisons que 21 % de bois vert dans notre production, sous forme de bois d’éclaircie et de bois endommagés. Néanmoins, nous soutenons actuellement l'un de nos principaux fournisseurs de bois frais dans le cadre d'un projet concret de renaturation. Le fournisseur - un grand propriétaire forestier public - a remplacé une monoculture d'épicéas par une zone alluviale et des forêts mixtes adaptées au site et résilientes. Il s'agit là d'un projet pilote. D'autres projets sont en cours de discussion avec d'autres fournisseurs de bois frais.
En 2023, nous avons rejoint l'initiative Biodiversity in Good Company, afin de nous engager, avec d'autres entreprises et acteurs politiques et sociaux, pour la protection et l'utilisation durable de la biodiversité. Cette initiative inclut des entreprises allemandes et japonaises de tous secteurs et de toutes dimensions. Les entreprises membres se sont engagées à prendre en compte la protection de la biodiversité dans leurs stratégies de durabilité et leur gestion de l'environnement. Elles ont signé la déclaration de principe , ainsi que l’engagement de Direction, établis au sein de cette initiative.
OBJECTIF 7
SIGNATURE DE NOTRE CODE DE CONDUITE DES FOURNISSEURS PAR 80% DE NOS FOURNISSEURS
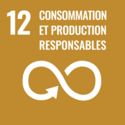
Nous nous sommes engagés à analyser systématiquement la durabilité de nos fournisseurs, pour mettre en place une chaîne d'approvisionnement responsable. Conformément à nos objectifs, nous avons mis en place en 2023 un cadre d'évaluation de la durabilité de nos fournisseurs. Ce cadre nous permettra de mieux systématiser notre approche et de rendre compte de manière transparente des améliorations en matière de durabilité dans notre chaîne d'approvisionnement. Nous continuerons à collecter des données lors de l’évaluation annuelle de nos fournisseurs. Elles nous permettront d’obtenir des indications sur le degré de maturité de leur gestion de la durabilité.
Nous nous sommes fixés de premiers objectifs mesurables en ce sens : 80 % de nos fournisseurs devront signer notre Code de conduite des fournisseurs d'ici 2025 et 95 % d'ici 2030. Au cours des années suivantes, nous utiliserons notre nouveau cadre d’évaluation, pour suivre et contrôler des indicateurs clés de performance (KPI) supplémentaires sur la durabilité des fournisseurs. Pour le choix de nos fournisseurs privilégiés, nous exigerons ensuite des évaluations normées, telles que celle d'EcoVadis.
TÉLÉCHARGEMENT
APPRENEZ-EN DAVANTAGE SUR LE DÉVELOPPEMENT DURABLE CHEZ PFLEIDERER
Ces thématiques peuvent également vous intéresser: